Products You May Like
New Space has for the last decade challenged the established design rules for spacecraft, and proved that is it possible to design and launch small spacecrafts at a fraction of the cost of traditional designs. OneWeb being one of the pioneers challenging the established supplier base using new thinking to drive down the cost and at the same time aiming for high reliability. The automotive industry is probably the industrialized segment that today has progressed furthest in establishing high reliability at low cost, and this was the initial inspiration behind the approach to reliability in spacecraft based on COTS. Another early pioneer showing what was possible was SkyBox imaging, building low cost satellites on a commercial basis, and are also one of the few that have executed a business plan resulting in major financial gain to the founders.

Sensonor, a MEMS sensor manufacturer with roots back to 1965, with a history in the defense, medical and automotive industries, in 2009 changed its focus to fully commit to the defense, industrial, and space markets. It set out to make Gyro and IMU modules with best practice from the automotive industry and with a technology base gained from several decades of manufacturing MEMS sensors. Building a business in the space segment was not on the initial roadmap. After introducing their first gyro module, targeting users in the defense and GNSS-navigation segment, a few customers including NASA, decided to fly these standard parts on several spacecraft technology evaluation missions. The gyro modules became part of the spacecraft’s attitude and orbit control system (AOCS). This serves a critical function in the launch/ deployment stage and also in operational control of the EO satellite systems. With favorable results, a range of papers and articles was published with reference to achieved results from the low-cost gyro modules, and several other New Space companies started flying the same parts. Soon the gyro module had become a standard component on their spacecraft for some builders. Users were not always willing or able to share their operational experience. This motivated Sensonor together with the Norwegian Space Agency and German-based Fraunhofer institute to design an experiment to test typical radiation environments experienced in LEO orbits. A relatively large number of gyro modules were used in the experiment and the plan was to test them until failure, to establish an understanding of the systems capabilities and safe operating conditions. Additionally, in the spirit of open innovation, Sensonor decided that the complete results with respect to capability would be published as an open document, to further support the spirit of New Space. It was never the plan to set out to make a space-qualified product, however to establish the capability of an existing design.
Since the design consists of multiple COTS components, it is still a risk in that raw material variations can cause uncertainty in the design of the complete product. Based on previous experience and to reduce risk, it is a design philosophy to utilize automotive-qualified components that have extremely low failure rates and high repeatability. Some spacecraft designers also mitigate COTS risk by sometimes operating multiple gyro modules in its spacecraft, based on risk acceptance. Following an inherited automotive change management system ensuring strict control and risk assessment of any changes made to the system design. Manufacturing the modules in a large series, with few variants ensures consistent reliability and quality, as well as keeping cost down.
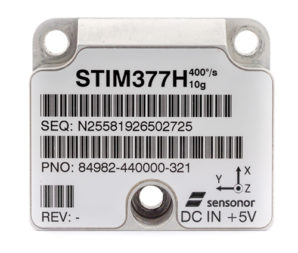
The majority of the systems manufactured by Sensonor are used in other industries as well as the space segment. The space segment accounts for less than 10% of its revenue and deliveries to space customers benefit from the same production line and processes that are identical for all customers.
IMU’s and Gyro modules play a key role in many defense and space applications, and customers have high requirements for reliability and long-term stability. Certain users have requirement for up to 30 years reliability, and the best way to approach this was by designing a hermetic part.
Having had a design in the market for almost a decade, it has set the standard with respect to size, weight and connectivity, meaning that the new design had to meet an established form, fit and function. The general requirement for a new hermetic gyro module was also reflected in the space segment.
The chosen design has a hermetic aluminum enclosure with a glass-to-metal sealed electrical micro-d connector and a laser-welded lid to secure long-term hermetic operation and to conform to MIL-STD-883J, Class H.
Making a hermetic sealed design in aluminum was more of a challenge that first anticipated, and required development of new technologies, material understanding and new processes for sealing and test.
Following 3 years of development, and a qualification program that tests for 10 and 20 years life expectancy the hermetic design is now released for production.
Additional requirements from the space community is included into the design, such as no other surface treatment than SurTec650, cleanroom packaging and a label that is optional for the user to attach to the part. The hermetic parts also address sensitivity to helium, that some customers have experienced, and that NASA also has published information on. Since certain launch vehicles have large amounts of free-flowing helium that may reach the payload, the hermetic unit makes the spacecraft design more robust for use on any launch vehicle. The hermetic gyro module benefits from the larger production runs resulting in only a marginal cost penalty for a hermetic solution whilst still supporting a space capable 3-axis gyro module for less than seven thousand dollars.
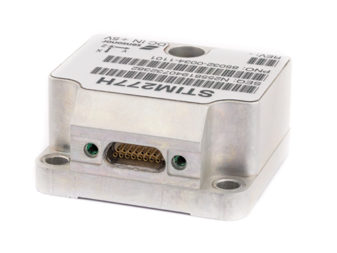
Sensonor will continue to service the space segment, and currently building the first prototypes for a new version IMU and gyro to address higher radiation levels. Several of the existing users would like to see a solution for space missions of longer duration and other orbits with higher radiation levels, while maintaining the same SWaP. Radiation testing of
this new design is planned for early 2021 with a possible product being qualified for production late 2022.
On a last note, it is also interesting to observe that Old Space has started to evaluate COTS for their missions and are adopting some of the thinking of New Space, or see the need of establishing product lines similar to those New Space has proven.